Add Boards¶
- Add a Top Level Board
- Record the Cables Feeding the Board
- Add a Sub-Main Board
- Record a Radial Circuit
- Record a Ring Main Circuit
- Add a Fuseway
- Copy and Paste Circuits
- Analyse Earth Cable Sizes
- Check the Board is Complete
- Add a Board Observation
- Add a Circuit Observation
Add a Top Level Board¶
- In the left tree, right-click on “Boards” then select “New” -> “Board”.
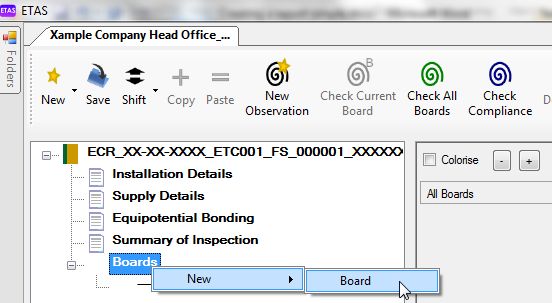
The New Board dialog is shown.
- From the “Type” drop-down list select “Distribution Board”.
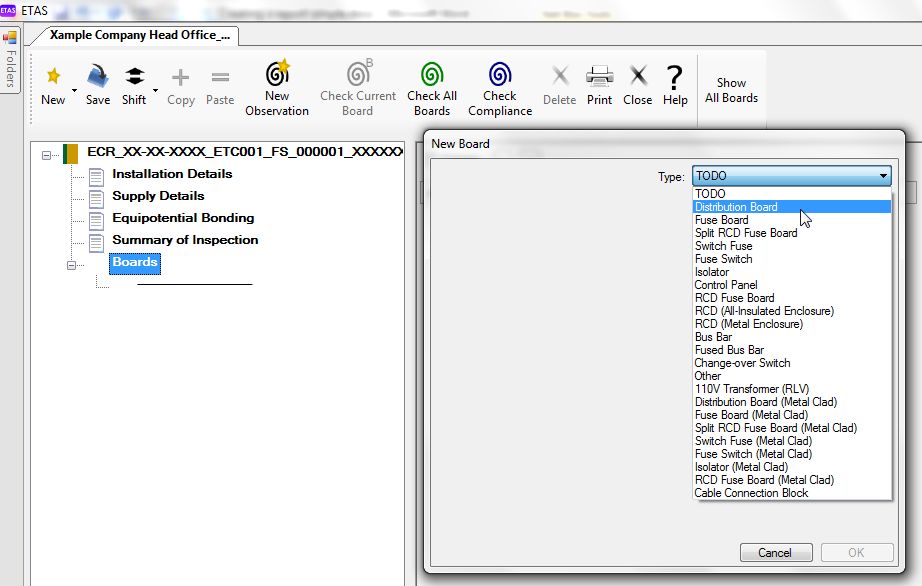
- Fill in the following information, then click OK.
Name/Asset Number
E.g. enter “1”. ETAS will automatically label this board “Distribution Board: 1” on the report.
Fuseways
E.g. enter 3
Supply Voltage, Phases, Neutral
ETAS will filter out options based on the upline supply type (e.g. if it was a 230volt supply, 400 V multi-phase choices would be greyed out). Because this is a 3-phase 4 wire supply, all the choices are possible. As this is the main distribution board at the source of supply, we will pick a 3-phase 4 wire distribution board.
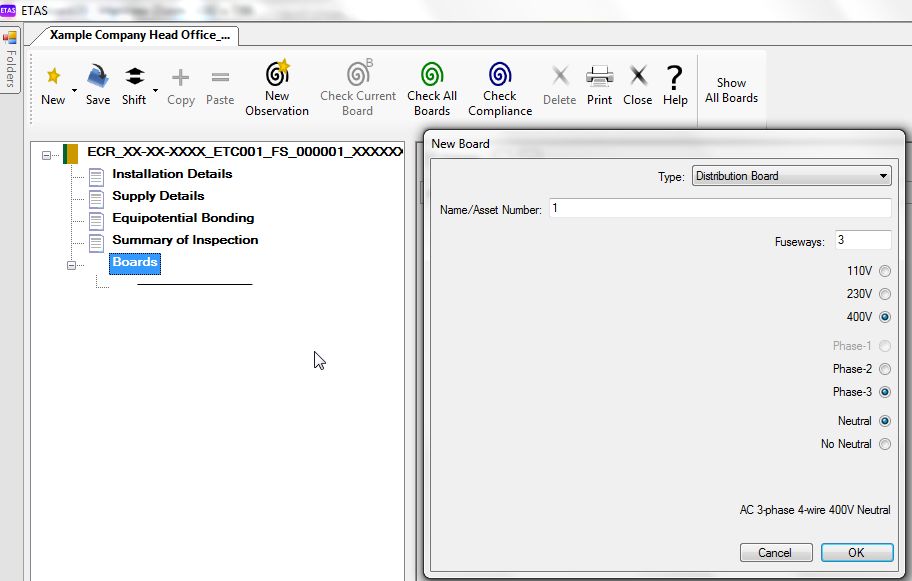
Verify that the new board was created and is shown selected in the left tree.
Note the line between the “Boards” item and the new board icon. The new board is shown below the line because you haven’t specified where it is fed from yet.
On the board “Specification” tab under “Board Fed From”, click Select.
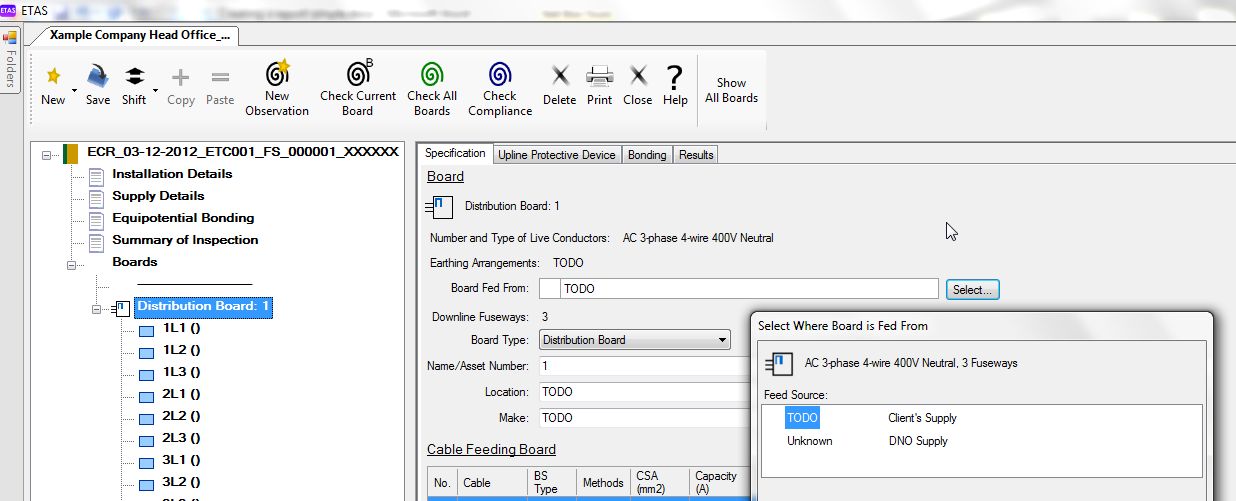
- As we know that the board is fed from the DNO, choose “DNO” in the pane and press “OK”.
- If you came across a distribution board etc. and you did not know where it was fed from and you chose “Unknown”, the board would remain below this line and an auto observation would be offered relating to the “Unknown” state when the |check compliance icon| button is pressed at the end of all data entry.
- Note the icon of distribution board. The icon shows that a 3-phase with neutral distribution board has been chosen with the 3 legs and “n” being shown to describe the phaseway group of the board.
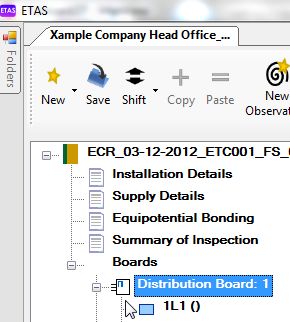
Record the Cables Feeding the Board¶
We will now enter the details of the cables supplying the distribution board.
On the board “Specification” tab under “Cable Feeding Board”, click “Edit”.
The “Phase/Earth Pair” dialog is displayed.
Specify a Single Core PVC/PVC (6181Y) <50.00 mm with a CSA of 35.00 mm. The CPC is an “Unbunched Copper Cable” with a CSA of 10.00 mm.
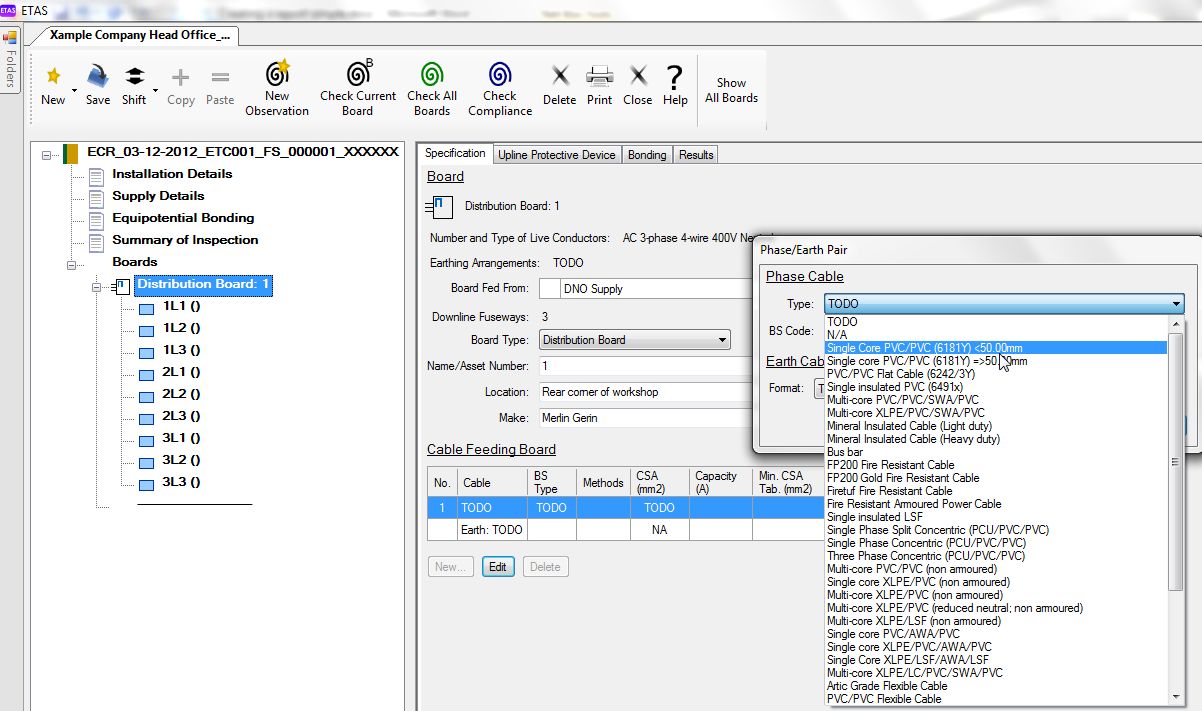
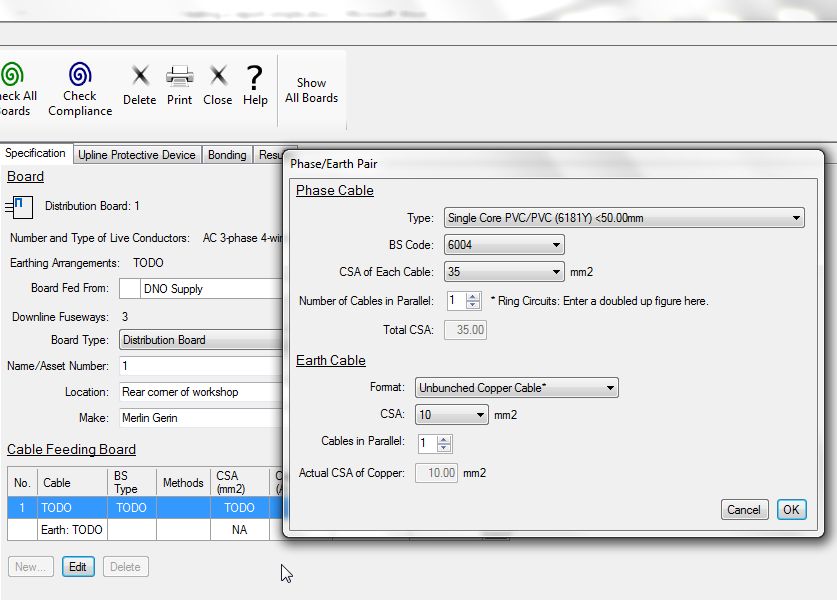
Note:
As per table 54.7 of the regulations, a cable where 16 > S > = 35 calls for a 16.00 mm CPC. The “Min CSA Adi (mm2)” field (adiabatic) cannot be automatically calculated at this time because the earthing arrangements of the board and the earth loop result have not been entered. Let us do that now.
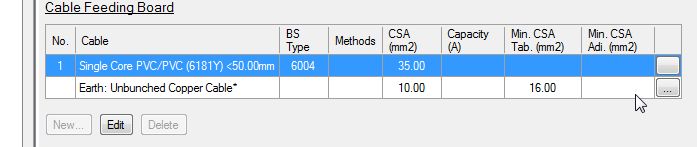
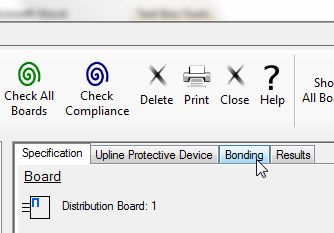
- Skip the “Upline Protective Device” tab (this shows the upline protective device(s) for information only, requiring no data to be entered) and click on the “Bonding” tab.
- Confirm that the distribution board is not outside the equipotential bonding area. We will deal with a distribution board outside of the equipotential zone later.
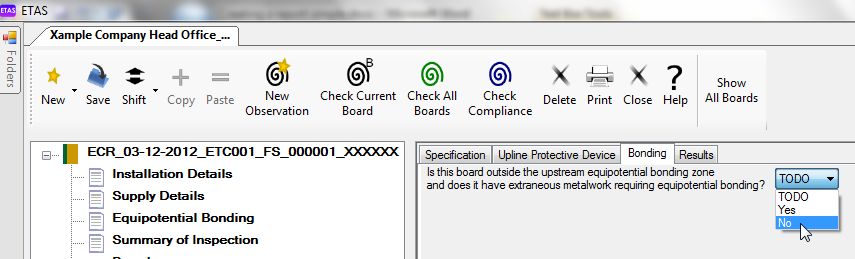
Select the “Results” tab and.
The maximum fault current is automatically calculated at this point. The highest reading of P-E, P-N and P-P-P is used to calculate the true prospective fault current, which in this case, is from a measured 14kA (this is actually P-P-P which is the P-P or P-N PFC reading taken x 2). The calculated maximum “let-through current” of the up-line protective device is now 5.4kA at this point. As this reading is calculated based upon a fault of negligible impedance it can only be taken as an approximation. This is used by the software to verify that the breaking capacity of the protective devices in this board and any further downstream, which are not let-through limiting devices (see note) are capable of withstanding the prospective fault current. (In this case, any protective device with a breaking capacity greater than 5.4kA in this board will pass even though the highest measured PFC is 14kA). Now enter the results.
Note:
Where protective devices e.g. MCBs, non-electronic MCCBs etc. that do not limit let-through energy, the software will look up-stream as far as the source of supply for devices that do limit the let-through energy and calculate and record at the point of measurement.
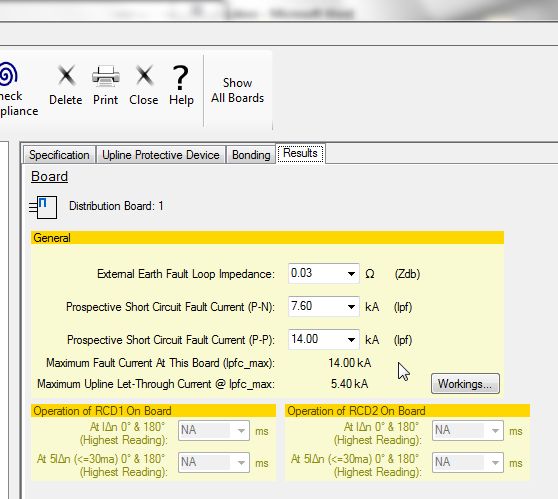
If you now go back to the “Specification” tab, you will see that now you have entered the earth loop result, the type of cable(s) and the method(s) of installation, the software has calculated the minimum CSA requirement for the CPC. In this instance, although it has failed the requirements as per Table 54.7 (16.00 mm required), but has passed using the adiabatic formula (5.09 mm required).
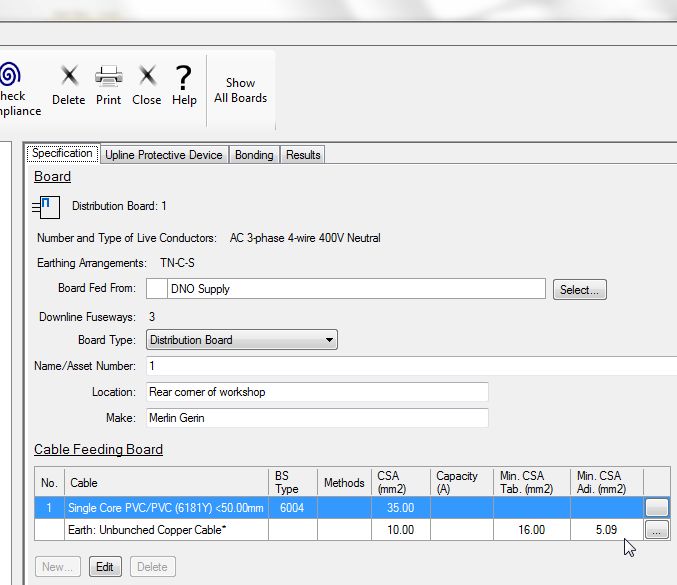
If you wish to view the calculation of the adiabatic formula, click on the tab to the right hand of the result as shown below by the position of the mouse pointer. The software will calculate the adiabatic formula against the “best” protective device in the “chain” - for example, if a circuit had a “chain” of up-line protective devices it may not pass on the protective device immediately upstream but may pass on a protective device further up. This would be true say, in the case of an RCD protecting the whole installation. In this particular case of course, the software has only the BS 88 160 amp supply fuse to consider.
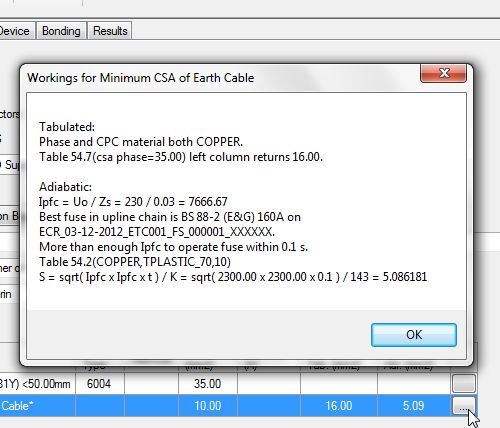
The distribution board details are now complete and we can move onto the circuits.
<link> Analyze Earth Cable Sized
Add a Sub-Main Board¶
Circuit 1L1 supplies a single-phase fuse board in the showroom.
- In the left tree, right click circuit 1L1 then select “New” -> “Board”.
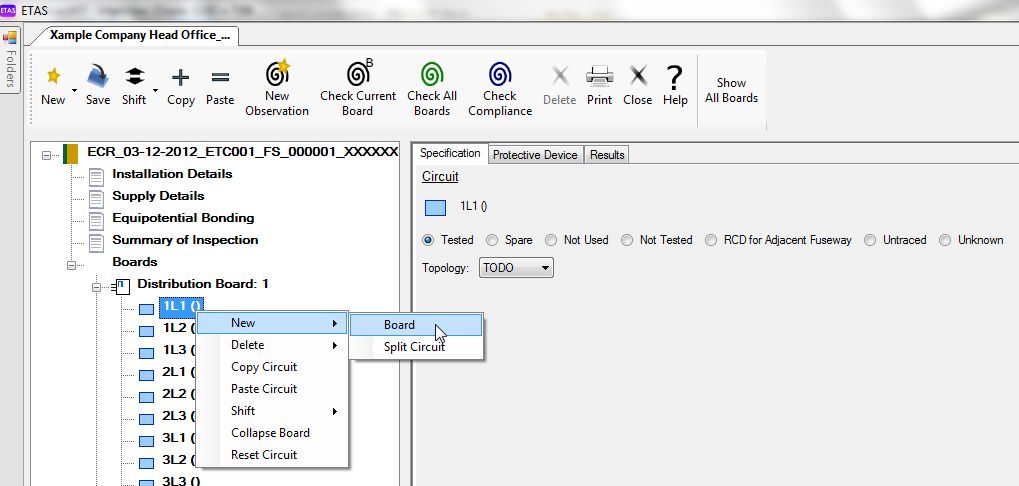
- Alternatively, on the circuit “Specification” tab under “Topology” select “Sub-Main”
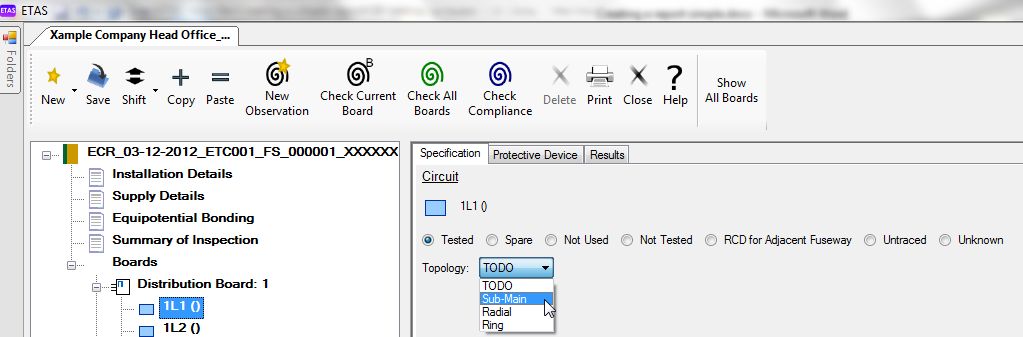
- In the “New Board” dialog box under “Type” select “Fuse Board”.
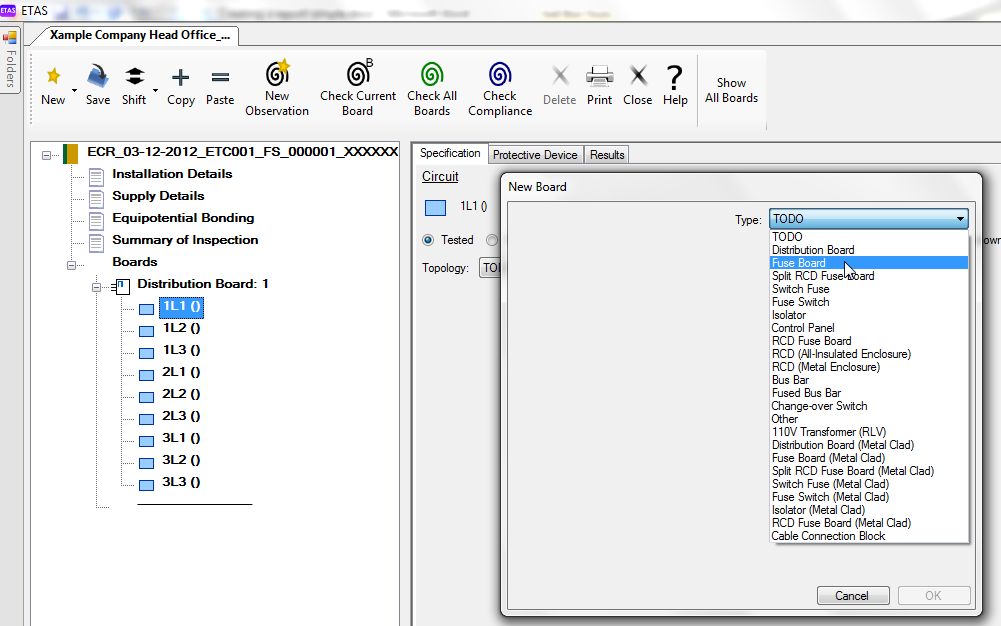
- Enter a name for the “board”, the number of fuseways and the phaseway details (in this case 230 V), then click OK.
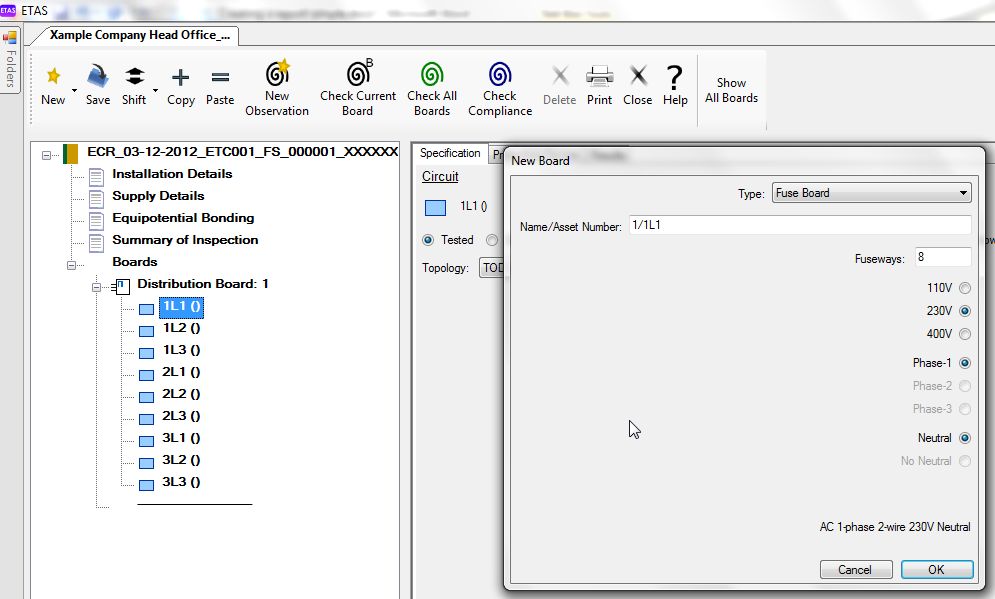
- The board icon changes to indicate a single-phase board.
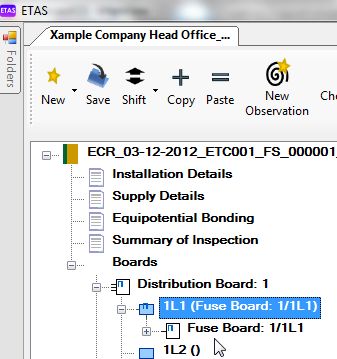
Specify the Cables Feeding the Sub-Main Board¶
- On the circuit “Specification” tab under “Circuit Cables in Series”, click “New” and choose the phase cable type supplying the single-phase fuse board. Let us choose a 25.00 mm 2-core 6346 armoured cable.
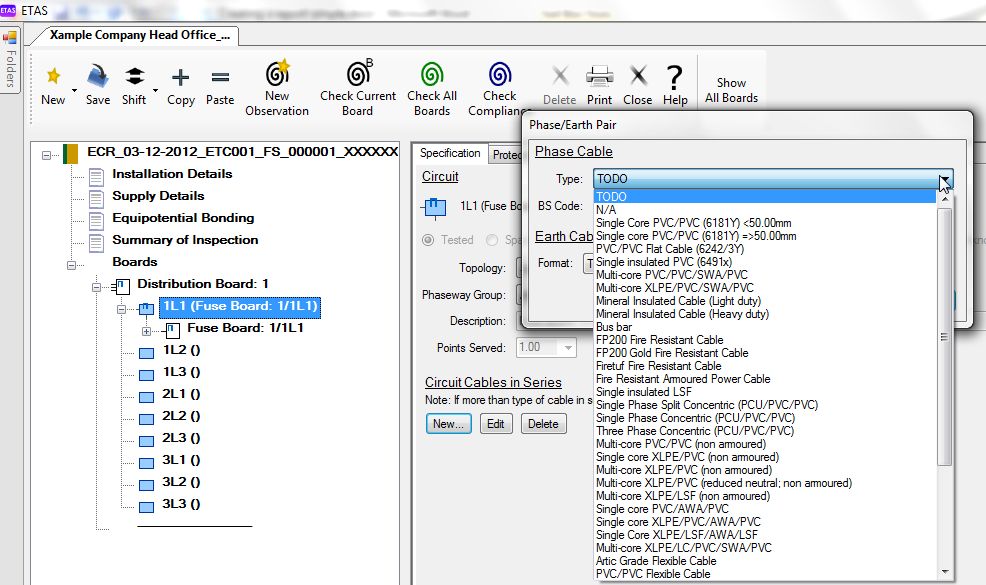
- If there were 2 x cables in parallel supplying this fuse board we would enter “2” in the “Number of Cables in Parallel” field; this would multiply the current carrying capacity of the supply. As it is only one cable, we will leave it as the default “1”.
- To the right of “Installation Methods” click “Select” to ascertain the current carrying capacity of the cable.
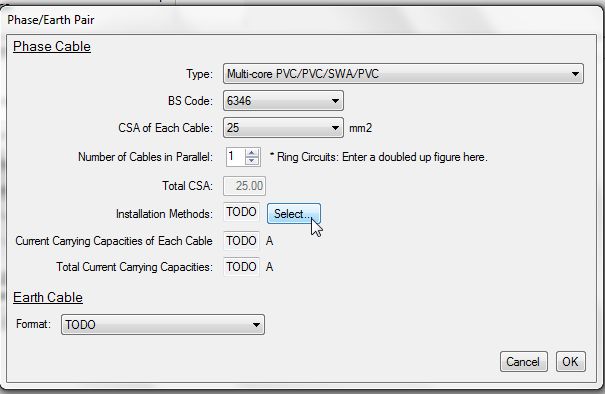
Note:
As this is a single phase cable, you are not able to inadvertently choose a 3/4-core 3-phase method of installation. You are able if required, to choose more than one method of installation. This cable is “clipped direct” only, therefore tick the relevant field.
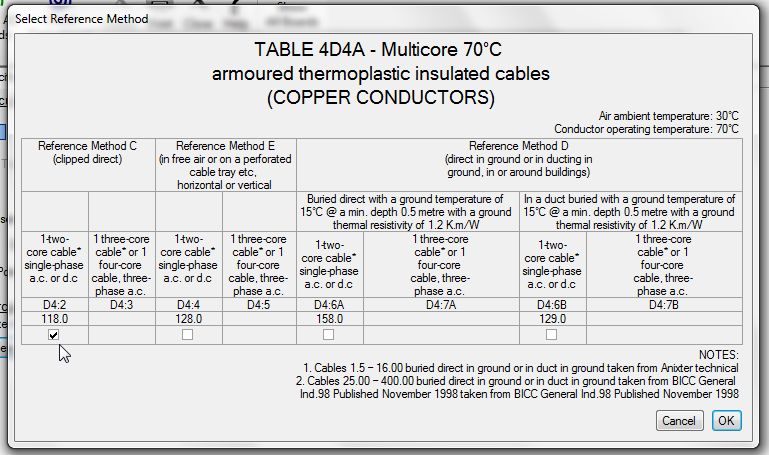
As you can see, the installation method and current carrying capacity has been recorded.
- Next we will choose the Earth Cable format. As we chose a 2-core SWA cable, in this instance, it is using the armouring as an earth.
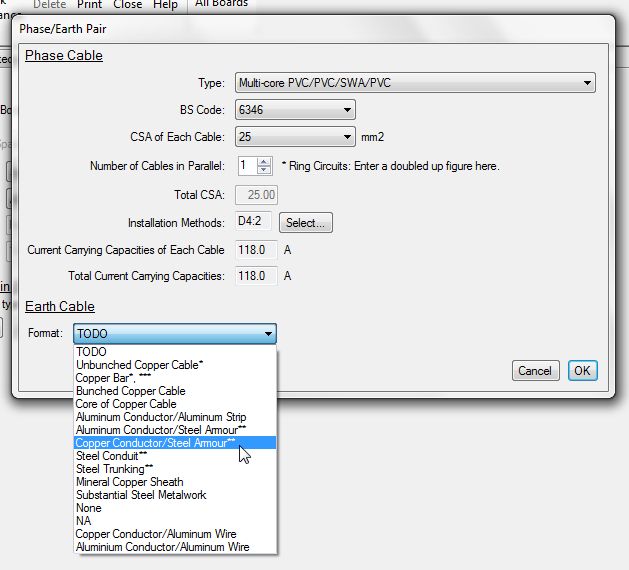
- You need to confirm the “BS Type”, the number of “Cores” and the “CSA” in case the earth is being supplied via another source. The “Actual CSA of Steel” has now been automatically calculated.
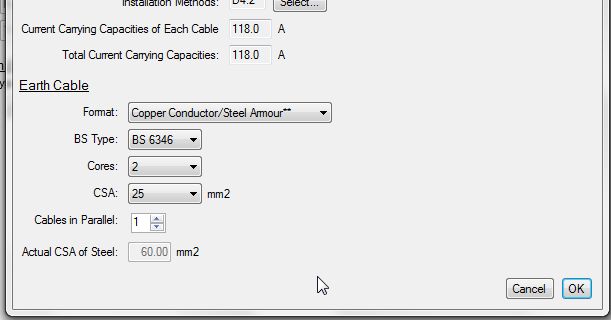
Choose the Protective Device¶
- Select the “Protective Device” tab and choose the fuse type.
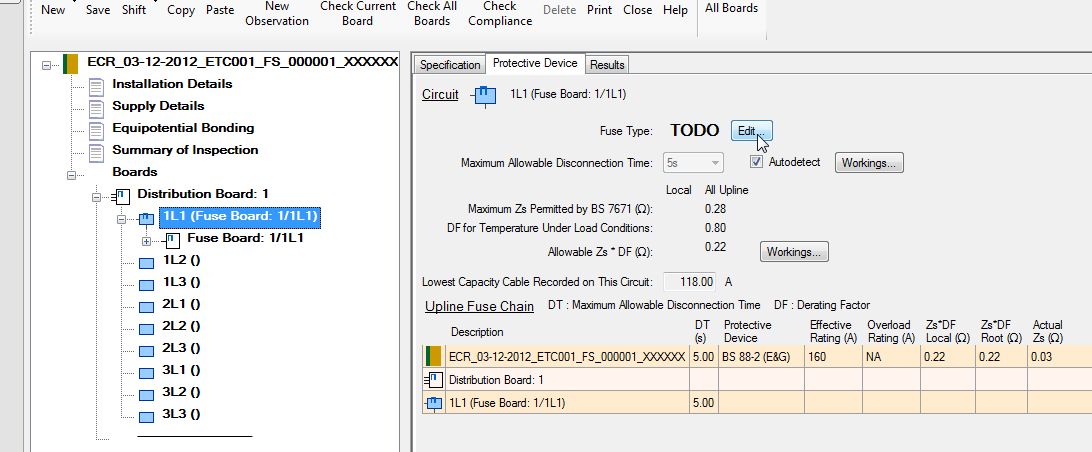
- Distribution board 1 is an MCCB distribution board having BS type 4752 MCCBs Therefore select BS 4752 Now we select the type of MCCB
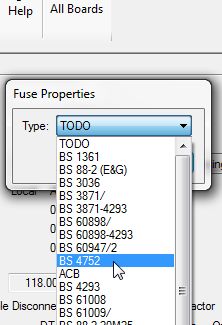
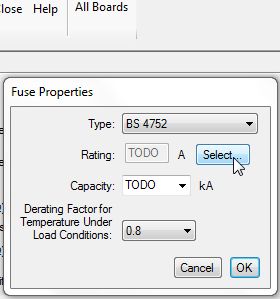
- The MCCB chosen is a thermal magnetic type having 2 x settings, overload and short circuit. Choose the type from the graphics. Now we enter the rating and settings of the device.
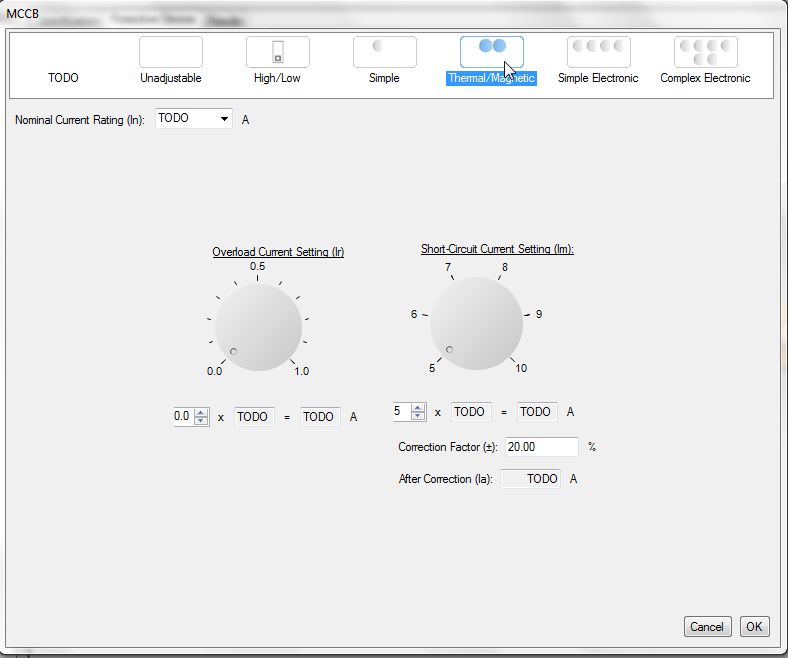
- Enter the current rating of the device (In), in this instance 125 amps.
- Drag the mouse on the dials to adjust their settings; in this case the overload current setting has been set to 87.5 amps and the short circuit current setting has been set to 9 x the nominal current rating (In). You can use the up/down arrows on the side of the field box instead of the dials if you choose.
- On the front of an MCCB there should be a correction factor; insert this reading in the “Correction Factor” field. If there is not a correction factor then leave it at its default setting of 20%.
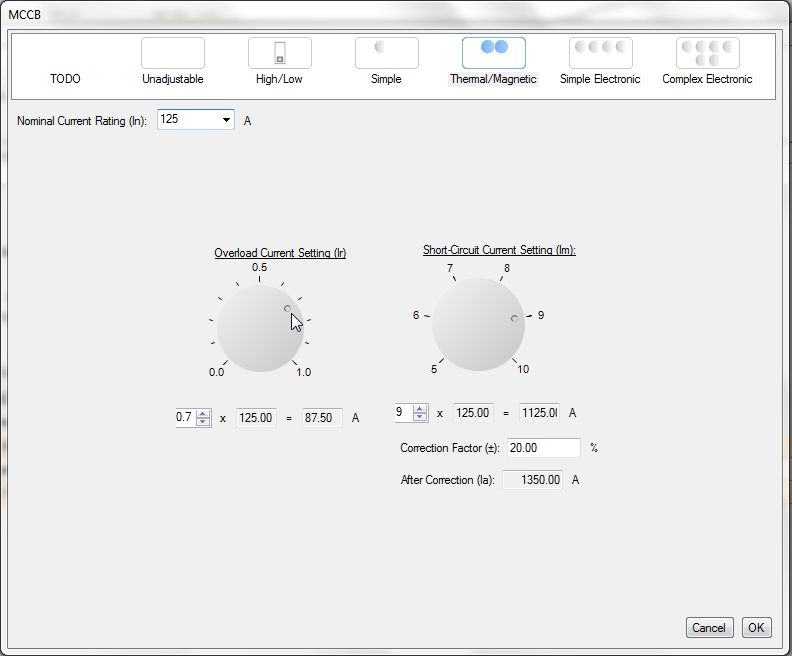
As you can see, the device requires 1125 amps + 20% = 1350 amps to operate in the required time of 5 seconds under a short circuit condition.
- Click OK then enter the breaking capacity of the MCCB.
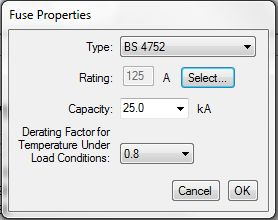
Fill in Circuit Results and View the Fuse Chain¶
- On the circuit “Results” tab, fill in all the missing fields marked TODO.
- You can either use your mouse between each field, which is rather laborious, or use your keyboard “Tab” key which is a lot quicker. Where fields require a word rather than a number, once you have tabbed to the field you can either use the first letter - for example, in the field “Polarity” press ‘P’ on and the keyboard “Pass” will appear or use the “down arrow” key on your keyboard and scroll through, this again is quicker than using your mouse.
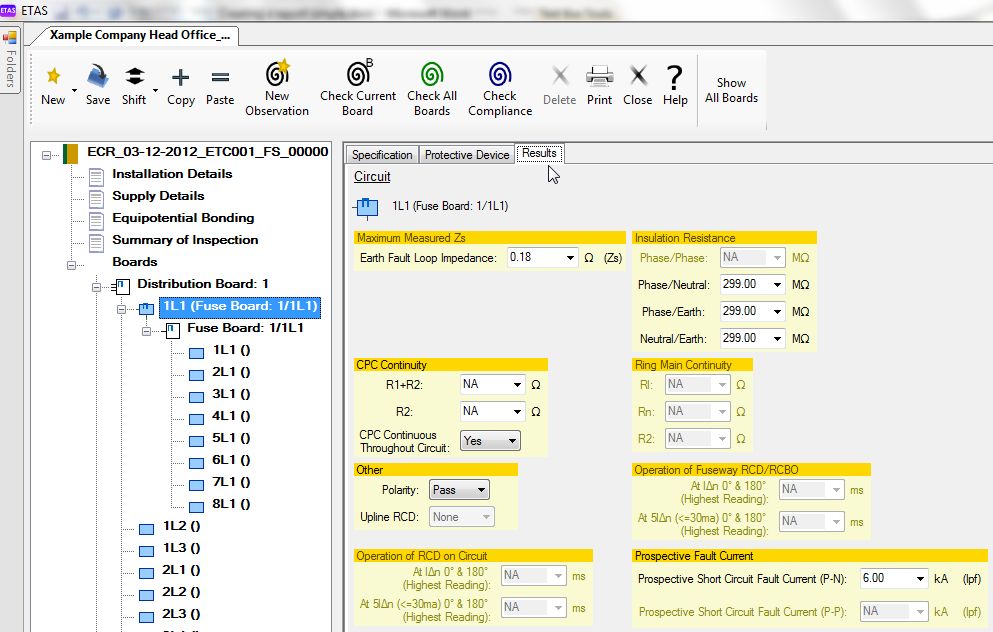
- You can now, if required, go to the “Protective Device” tab in the right hand screen and view the fuse “chain” with all the completed information.
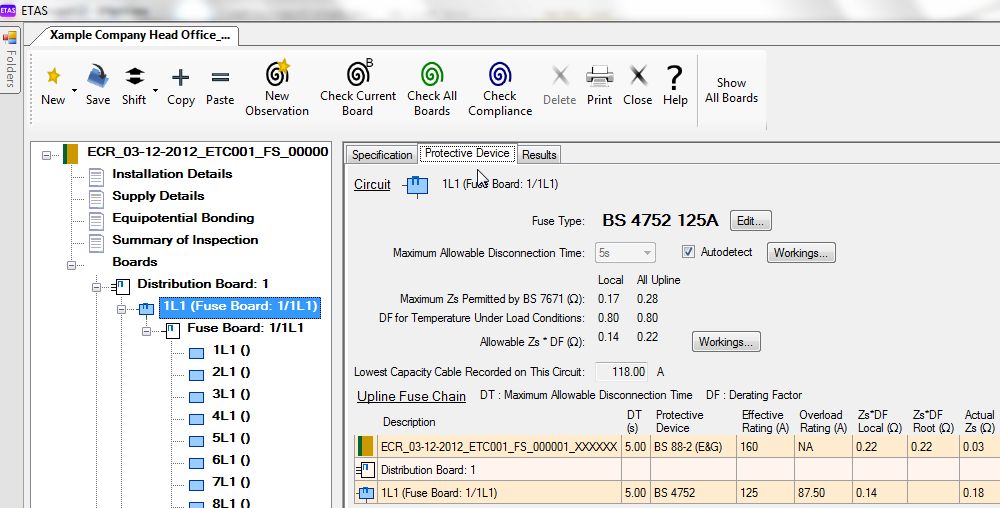
It is worth now spending a little time to show how the software uses the information recorded and why we view the “chain” of protective devices.
The maximum Zs permitted for the “Local” protective device is 0.17/0.8 (de-rating factor) = Allowable Zs of 0.14 Ω. It also shows the maximum Zs permitted of the best of “All Upline” devices. In this case we only have the 160 amp supply fuse which is 0.28/0.8 = 0.22 Ω. We have recorded an earth loop value of 0.18 Ω; the “Local” protective device requires a maximum of 0.14 Ω to operate the device in the required time of 5 seconds. Therefore this circuit fails for earth fault protection, or does it?
The software will look upstream no matter how far downstream the circuit in question is, to see if an up-line device will operate in the time required. In this case the 160 amp supply fuse requires a maximum of 0.22 Ω at 5 seconds, therefore, for earth fault protection it passes and is safe for continued use and an automatic C2 observation will not be “offered” to be recorded. If, in the case of a circuit having a maximum disconnection time of 0.4 seconds, the “local” and all up-line devices will show the “Allowable Zs” for a 0.4 second disconnection time and the software will calculate accordingly.
The software will also assess the size of the protective device for the current carrying capacity of the cable. If, as in this case, the current carrying capacity of the cable is 118 amps and the MCCB did not have an adjustable overload setting, therefore rated at 125 A it would “Fail”. If any upstream devices including their overloads (if applicable) were rated less than 118 amps it would pass for overload protection and again, an automatic C2 observation will not be “offered” to be recorded. In either case, subject to a risk assessment it does not preclude discrimination, which if applicable, may only merit a C3 observation.
Fill in Board Results and Analyse Fault Current¶
- Now we fill out the details for this fuse board. Where data has been previously recorded and is required here, for example the Name/Asset Number of the “board”, the P-N Prospective fault current reading which is entered on the supplying circuit and if the “Bonding Details” = “No”, the “External Earth fault loop Impedance” data is already entered for you to save time and alleviate possible transcription errors.

- A quick reminder of “Let-through energy” and breaking capacity. The software will now analyse the highest prospective fault current at this point. As the direct up-line device (MCCB) does not have “let-through” energy protection it will go up-line to the best device available and calculate accordingly. If you tab on “Workings” it will bring up the calculation(s) which in this case is the BS 88 160 amp supply fuse.
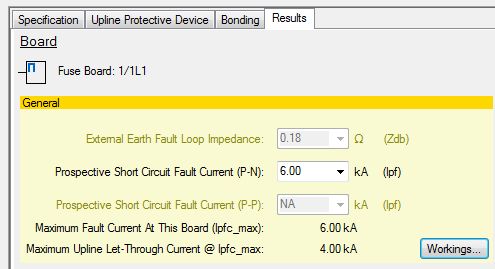
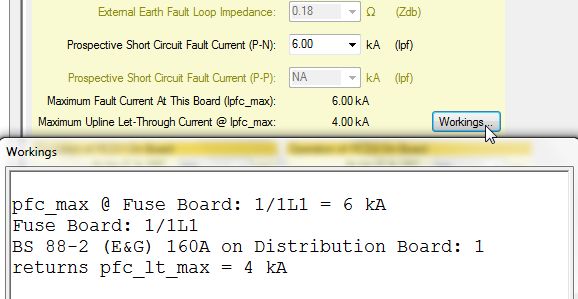
- Any protective device downstream of this point, having a breaking capacity of 4kA or more will pass regardless whether any prospective fault currents recorded or measured downstream are in excess of 4kA.
We will now move onto the circuits.
Record a Radial Circuit¶
Fuseway 1L1 supplies a lighting circuit, which is wired in a 1.5 mm 6242Y cable protected by a 10 amp MCB.
- On the circuit “Specification” tab under “Topology” select “Radial”.
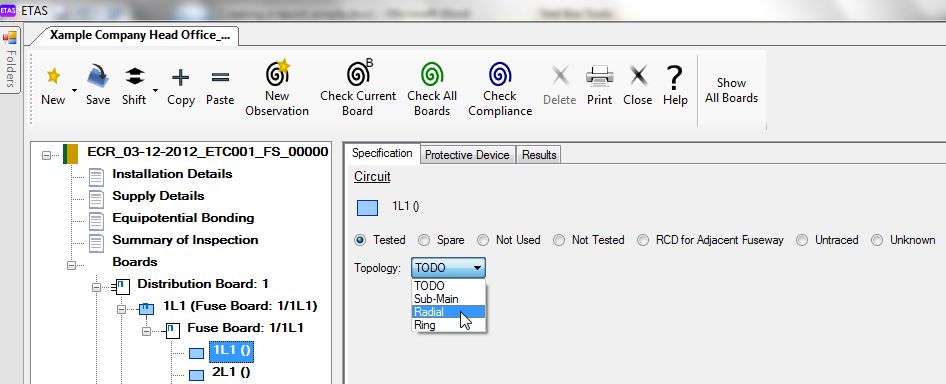
- Under “Phaseway Group” choose “AC 1-phase 2-wire 230V Neutral”. Since this is a single phase board the choice is automatically limited.
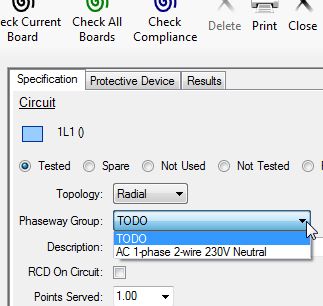
- Now enter the “Description” of the circuit.
- Click on “New” to choose the cable type. In this case, as stated above, it is a 6242Y cable.
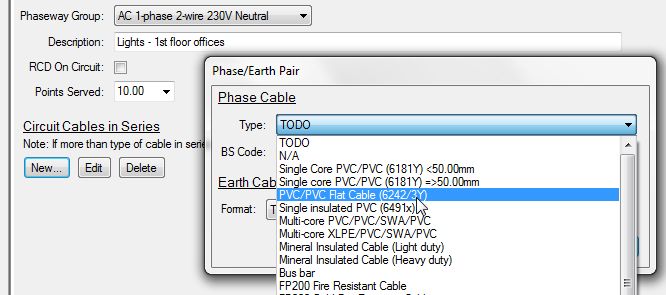

- We will now enter the size of the cable. As we have chosen a 6242Y cable, the software will automatically fill in the CPC details (these details may be over-written).
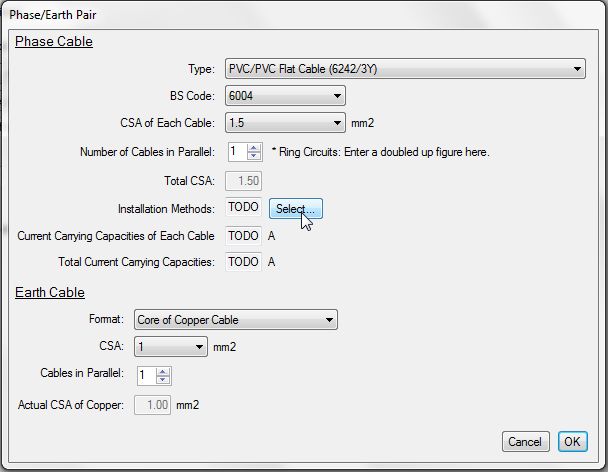
Next, we will choose the “Installation Method”.
In this instance we have chosen two methods of installation. The software will use the lowest rated method for calculation.
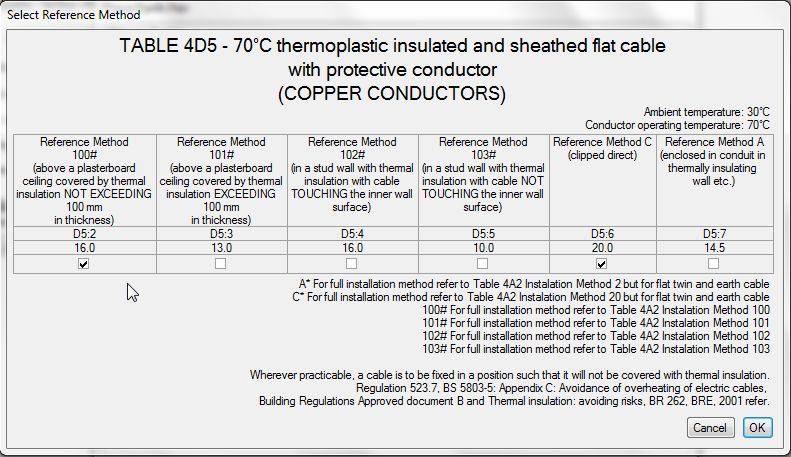
- Select the “Protective Device” tab and enter the protective device details.
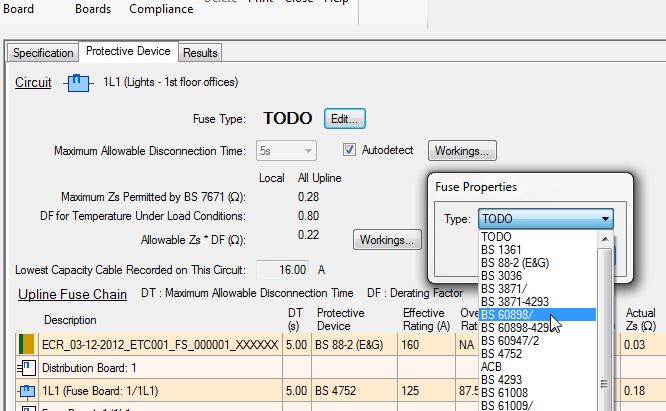
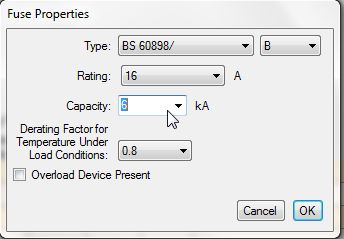
- Now select the “Results” tab and by using the tabbing key enter the results. In this instance we have not been able to carry out the Phase Neutral insulation resistance test. Once tabbed into the field, type in “U” or use the down arrow key and choose “UTT”, or you can use your mouse. As this is an Electrical Condition Report you would not be expected to disconnect every fitting to enable a Phase to Neutral insulation resistance test. As such, the software will ignore the “UTT” (this also applies to a Phase to Phase insulation resistance test if on a multi-phase circuit). If a low reading was recorded, the software will offer an automatic observation when a “Compliance” check is carried out.
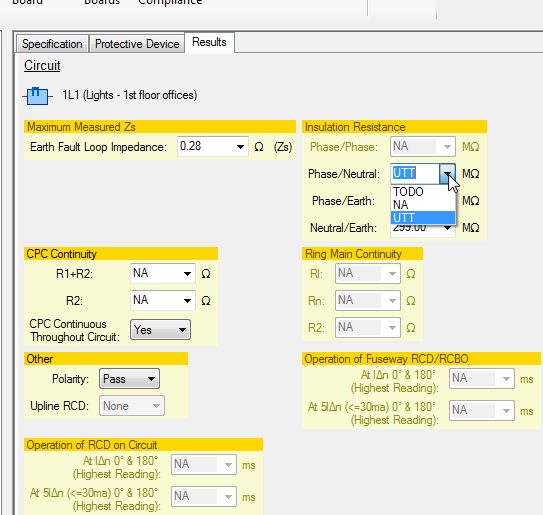
Take note of the earth loops in relation to the “Chain”. The lighting circuit requires a 0.4 second disconnection time (DT), which is verified if you go left in the row from the mouse pointer. If you follow the column “Zs*DF Root” up from the mouse pointer, the figures shown are the earth loops required for each device in the “chain” (0.14, 0.11) to operate within 0.4 second. See note above on “how the software uses the information………”
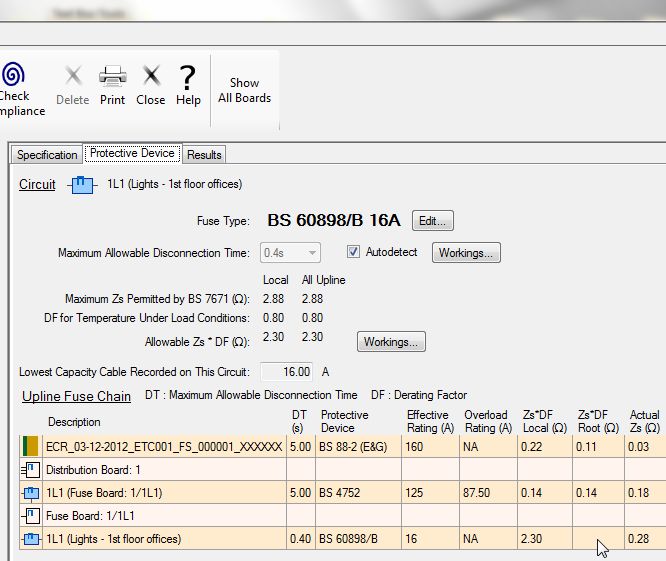
That is the first radial circuit complete!
We will now use the “copy” and “paste” function. We have a similar circuit feeding the ground floor lights, being wired in 1.5 mm 6242Y cable and having the same type and size protective device. The only items too change are the circuit description and any differing result readings. This circuit is fed from fuseway 3L1. Highlight the circuit in the left hand pane and right click your mouse and choose “Copy” or go up to the toolbar and click on “Copy”. Now highlight the appropriate circuit (3L1) and right click your mouse and choose “Paste”, or go up to the toolbar and click on “Paste” and there it is, pasted in.
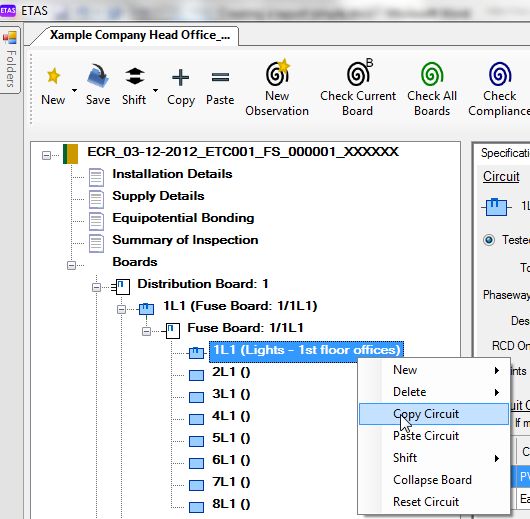
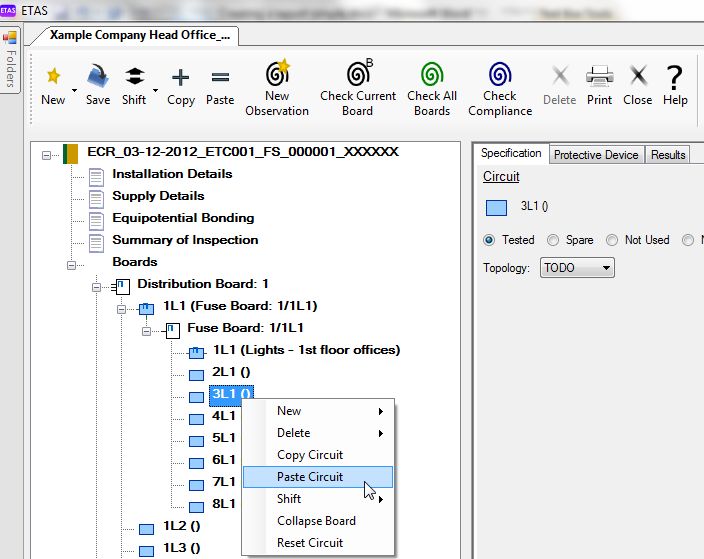
Now go to the “Description” field on circuit 3L1, highlight and make the change to “ground” and go to the “Results” tab and any differing result readings.
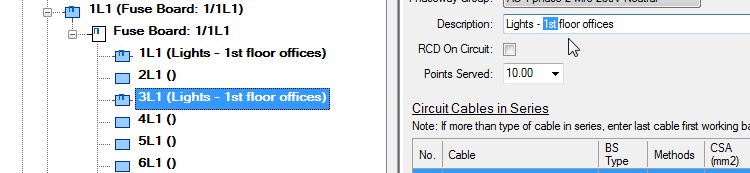
That’s it - fuseway 3L1 all done.
Note:
You can also copy and paste circuit details between boards, this is obviously subject to the phase way group (the software recognises a multi-phase circuit and will not allow you to paste a multi-phase circuit to a single phase board or a 3-PN circuit to a 3-P board etc.)
Record a Ring Main Circuit¶
Let us now enter a Ring main.
- On the circuit “Specification” tab under “Topology” select “Ring”.
- When entering the phase cable details, the software recognises that you have chosen “Ring” and that you have stated in this case, a “6242Y” cable. The software will automatically enter the “Number of Cables in Parallel” which will be 2. As it is a 6242Y cable, it will also enter the CPC size automatically and as it is a “Ring” enter 2 automatically in “Cables in Parallel” (this may be overwritten).
- If the ring was not wired in 6242Y cables, it would leave the earth cable details to be entered manually - if for example, conduit was being used as the CPC.
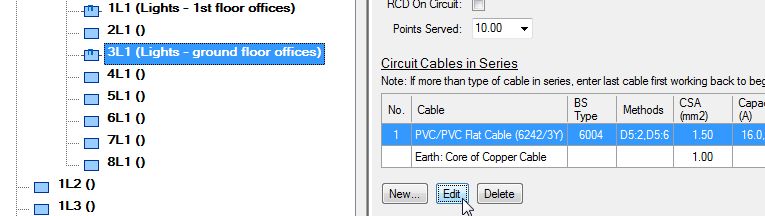
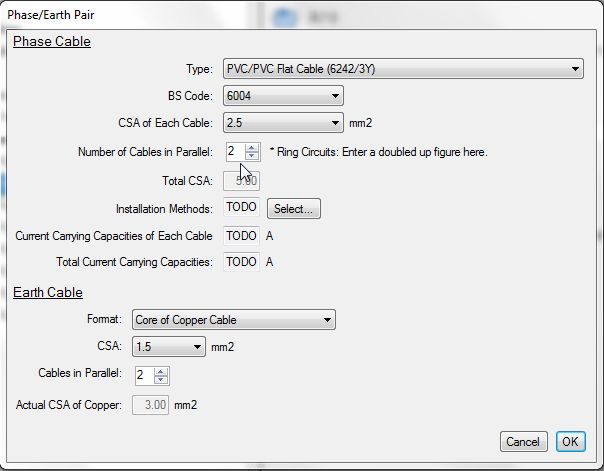
- As the software recognises that a Ring has been chosen as the “Topology”, the “Ring Main Continuity” readings are no longer greyed out under the “Results” tab. If conduit, mineral insulated or SWA etc. was being used as an earth, enter “NA” for the Ring Main Continuity “R2” reading. The software will recognise the earth format and will ignore the Ring Main Continuity R2 “NA” reading.
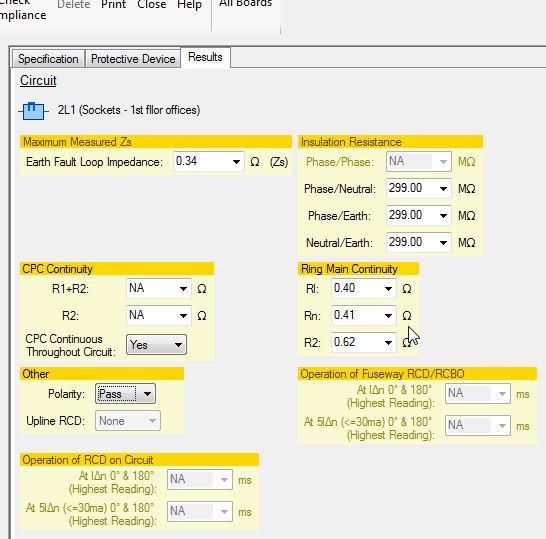
Add a Fuseway¶
When setting up the fuse board, if you make a mistake by entering “8” fuseways where in fact there were “9” for example.
- In the left tree right-click the board then select “New” -> “Fuseway”.
- This will add an additional fuseway onto the end, which will be 9L1. You will need to carry out this action for each additional fuseway required.
- For a multi-phase distribution board, the adding of a fuseway will add a complete phase group each time (*L1, *L2 and *L3).
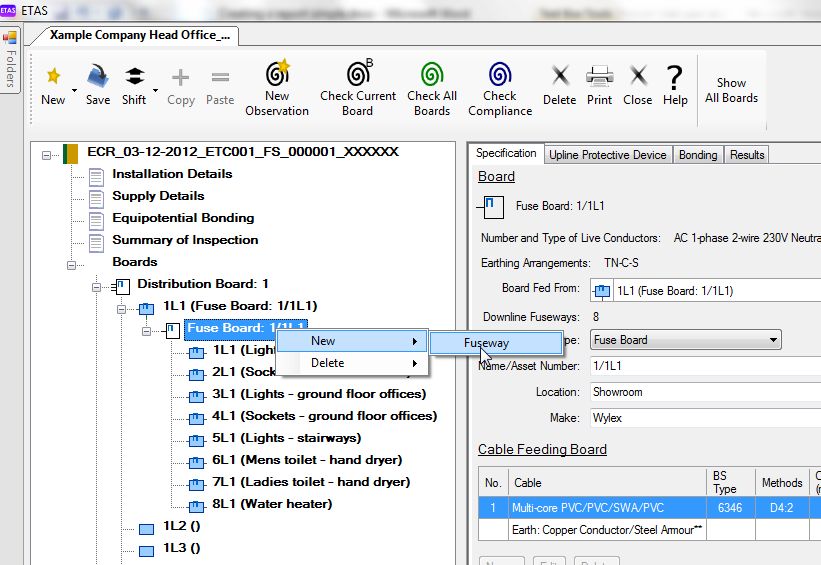
- You can delete a fuseway in the same way, being aware that if it is a multiphase board, the complete phase group will be deleted each time (*L1, *L2 and *L3).
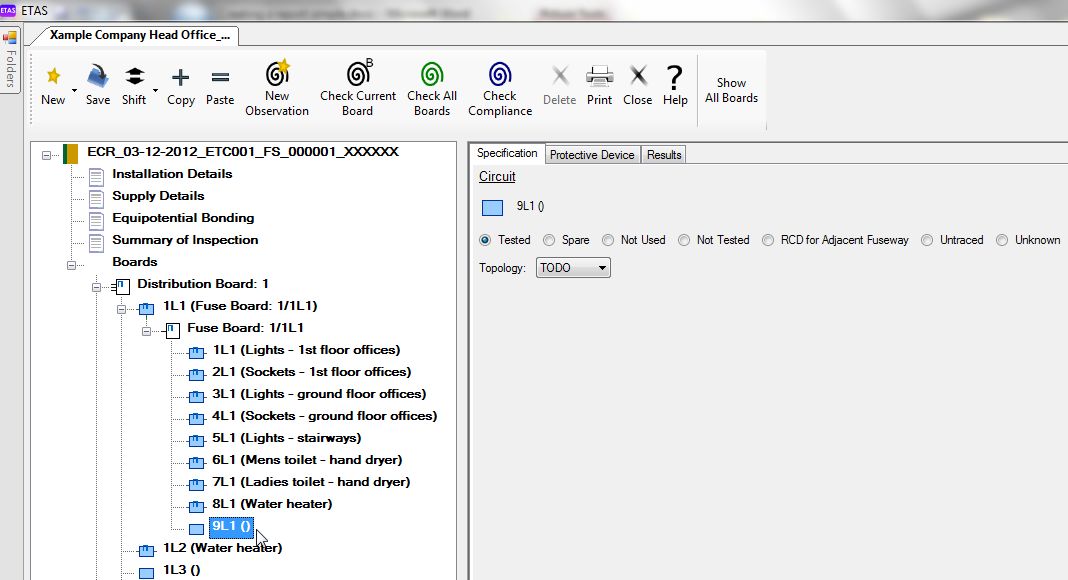
Copy and Paste Circuits¶
Imagine you make a mistake when entering a fuseway.
Example
You have recorded circuits on the wrong fuseways. “Lights - stairways” entered on fuseway 5L1 should have been entered on fuse way 8L1, and “Water heater” entered on fuseway 8L1 should be on fuseway 5L1 .
You can correct this easily several ways without having to enter the data for both circuits again.
If you have a “Spare” fuseway copy one of the circuits to this fuseway. For example, let’s copy and paste circuit “5L1 (Lights - stairway)” onto circuit 9L1.
- In the left tree, right-click circuit 5L1 then select “Copy Circuit”.
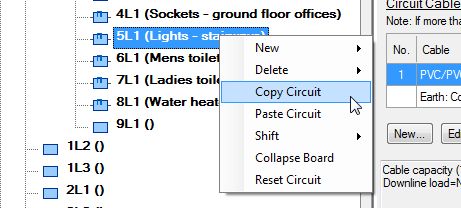
- In the left tree, right-click circuit 9L1 then select “Paste Circuit”.

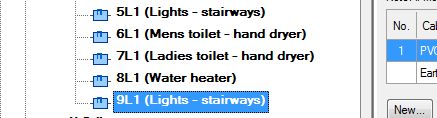
- In the same way as above, now copy and paste circuit “8L1 Water heater” onto 5L1 (this will completely over-write the original circuit).
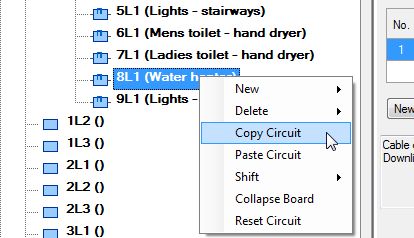
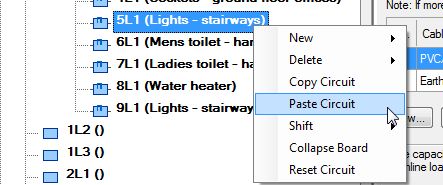
4. Now go back to the fuseway marked originally as “Spare” and re-assign it as a “Spare” under the “Specification” tab.
- If you do not have a spare fuseway, you can copy and paste one of the circuits to another board if you have a fuseway without any data entered, or if there is a fuseway marked “Spare” using it as a temporary “note pad”.
- Alternatively you can “Add” another fuseway to the board in question as described above and use this as a temporary “notepad”, not forgetting to delete this temporary fuseway of course, when finished.
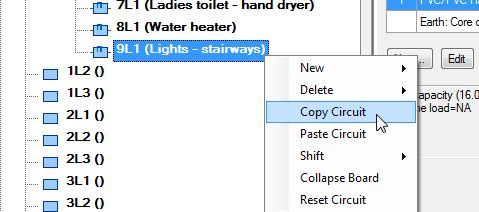
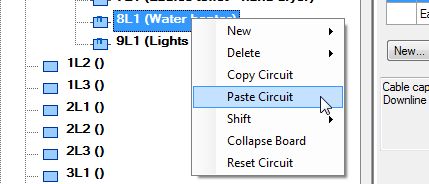
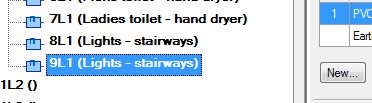
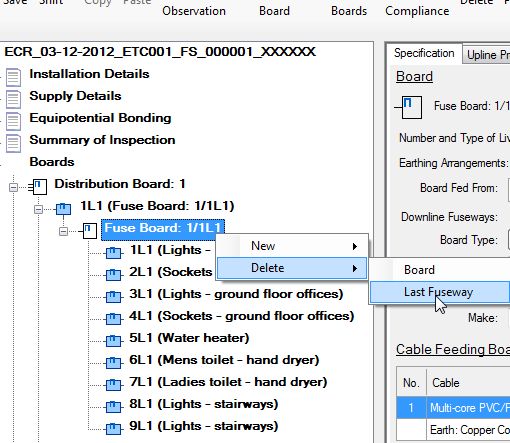
Analyse Earth Cable Sizes¶
ETAS will try and calculate the minimum size of CPC required and display the result on the board “Specification” tab providing you have filled in the following:
- Earth loop result
- Type of cable(s)
- Method(s) of installation
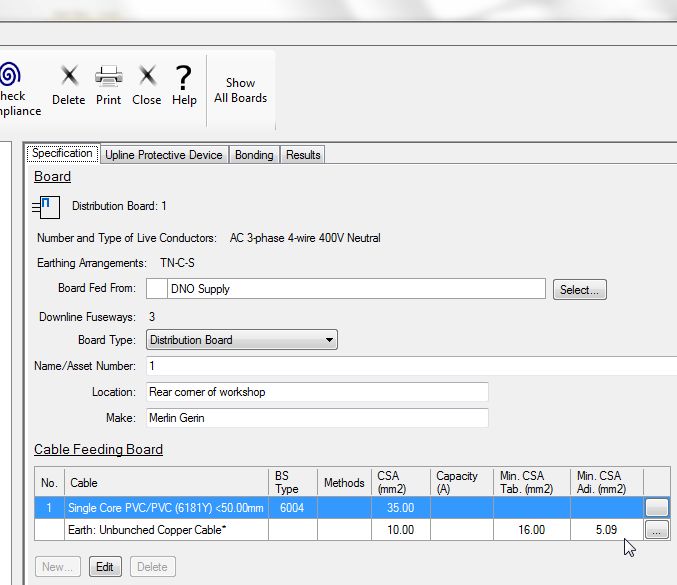
In the screenshot above, although the cable has failed as per Table 54.7 (16.00 mm required), it has passed using the adiabatic formula (5.09 mm required).
If you wish to view the calculation of the adiabatic formula, click on the tab to the right hand of the result as shown below by the position of the mouse pointer. The software will calculate the adiabatic formula against the “best” protective device in the “chain” - for example, if a circuit had a “chain” of up-line protective devices it may not pass on the protective device immediately upstream but may pass on a protective device further up. This would be true say, in the case of an RCD protecting the whole installation. In this particular case of course, the software has only the BS 88 160 amp supply fuse to consider.
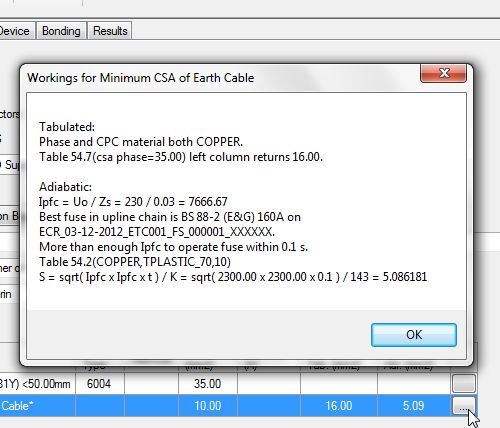
Check the Board is Complete¶
Now that we assume that this fuse board has all the data applied, we can verify this.
- In the left tree, select the board or a circuit within the board, then click |check board icon| (Check Current Board).
- This will only check the current board in question. You do have a “Check All Boards”, but at this time is pointless because we have several boards left to do.
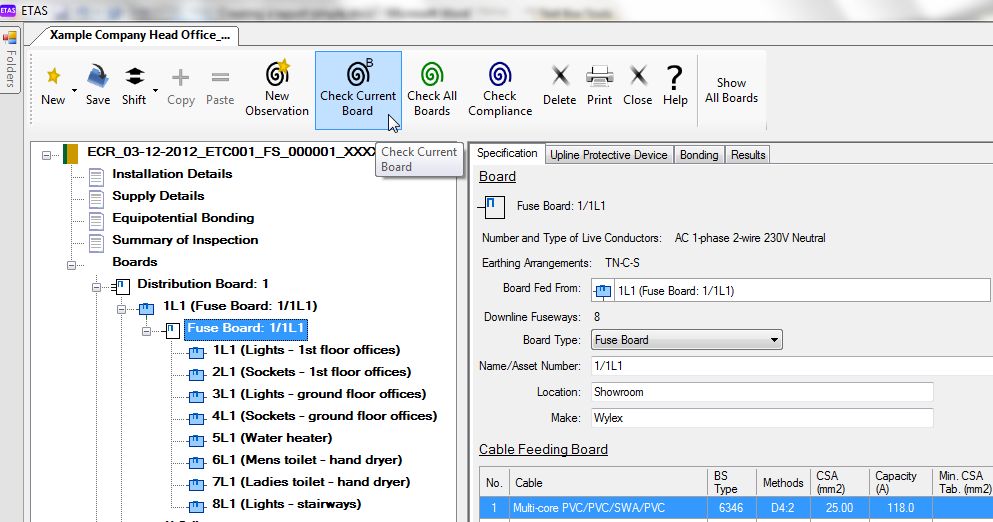
- There is only one piece of data missing listed in the bottom right hand pane. The software will take you straight to the missing field on the “Results” tab, de-noted by a flashing red icon. If there was more than one item missing, by clicking with your mouse on the chosen missing data in the bottom right hand pane, it will take you straight to the relevant field - all fuse ways in the left hand pane will have a red flashing icon against it if there is missing data on its fuseway.
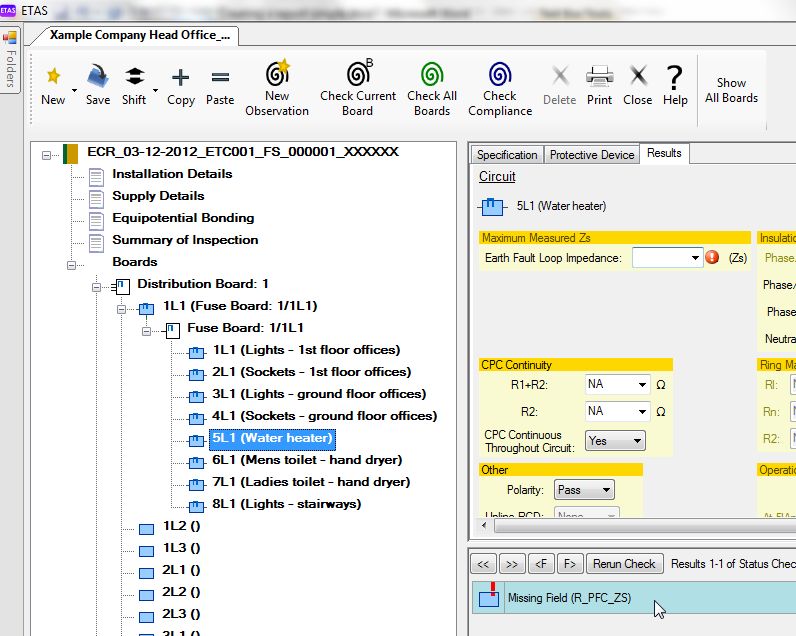
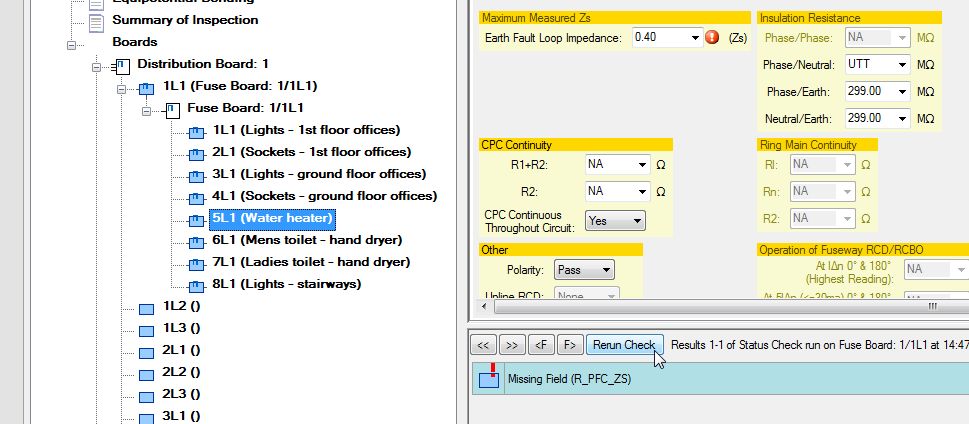
- Enter any missing data then click the |check board icon| icon or “Rerun Check” button.
- If all data has been entered the “Success” pane will appear. That’s it, fuse board complete!
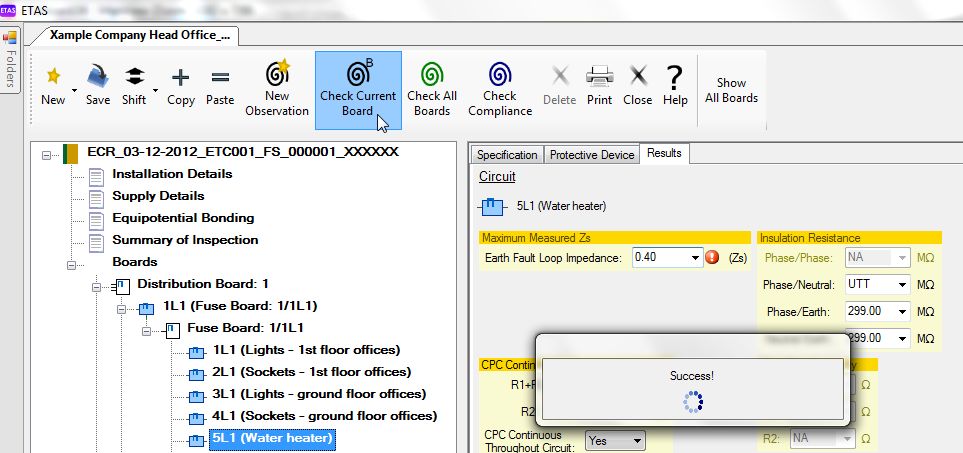
Add a Board Observation¶
Before we enter “Manual observations”, we need to talk about “Auto observations” and how they work within the software. Auto observations will not be offered until the |check compliance icon| button is clicked and all data for the installation is entered. If you click the |check compliance icon| button and there is data missing, all missing data will show in the bottom right hand pane (same action as “Check All Boards”). Auto observations are calculated and may rely on data either upstream or downstream to “Pass” - for example: Let’s say we had a single phase fuse board fed via a 16.00 mm cable with a rated current carrying capacity of 89 amps. The fuse upstream is a 100 amps device and therefore, it appears that the protective device is too large for the cable. Downstream The software will add up all the fuseways in the supplied fuse board at their face value, except for ring mains which are calculated at 26 amps. If the total of fuseways is less than 89 amps, there is no risk of over load to the 16.00 mm cable and therefore an auto observation will not be offered. For a multi-phase distribution board, each phase group is totalled up, so you may have 1 x phase having a total load greater than the current carrying capacity of the cable and therefore at risk of over load, with the 2 remaining phases having a total less than the current carrying capacity of the cable. In this instance the software will offer an auto observation for the relevant overloaded phase(s).
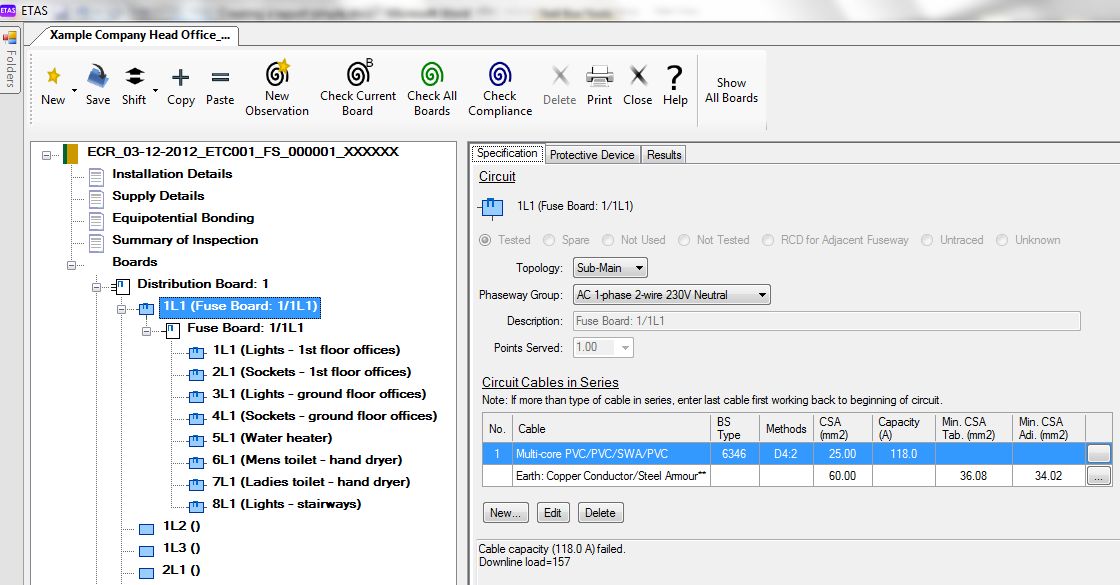
Here is a prime example from the data entered. We have a 25.00 mm cable rated 118 A. The upstream device is rated at 125 amps. The software having looked upstream as far as the DNO fuse and not finding a fuse less than 118 amps will now calculate the total face value of each fuseway within the fuse board (except for ring mains where a 30 or 32 amp devices are calculated at 26 amps). The total potential load = 157 amps, therefore there is a risk of overload and the software will offer the required auto observation when a “Compliance Check” is carried out. If the total of the face values of the fuseways was less than 118 amps there would not be a risk of overload and an auto observation would not be offered.
- Note:
- For the software to be able to calculate for potential overload, all “Untraced”,”Not Tested” and “Unknown” circuits will need their protective device details entered. The software will calculate the total load as far downstream as the last fuseway in the case of boards being fed from other boards in the chain.
Upstream
Let’s say we had a 16.00 mm cable which by its method of installation is rated at 89 amps. The cable is supplying a switch fuse which in turn is supplying a 10.00 mm mineral insulated cable having a current carrying capacity of 65 amps. The upstream protective device supplying the switch fuse and protecting the first 16.00 mm cable is rated at 63 amps. The fuses in the second switch fuse are rated at 100 amps. (Although the downstream devices are bigger than the upstream device, there may not be a risk from lack of discrimination - the switch fuse may be being used solely for isolation purposes). The software recognises that the 100 amp devices are too large for the second 10.00 mm cable but looks upstream to see if there is a suitable device and finds that the 63 amp device is low enough for overload protection. Therefore, there is not a risk of overload of the second 10.00 mm cable. The same would be in the case of an earth loop reading too high for the immediate upstream protective device, if there is a protective device further upstream, which by its size or type allows a higher earth loop reading; this is especially true if there is an RCD further upstream which will operate well within the required time. Therefore, all data for the installation needs to be recorded before an auto observation can be offered
- Select the board or a circuit on the board, then click the |new observation icon| button.
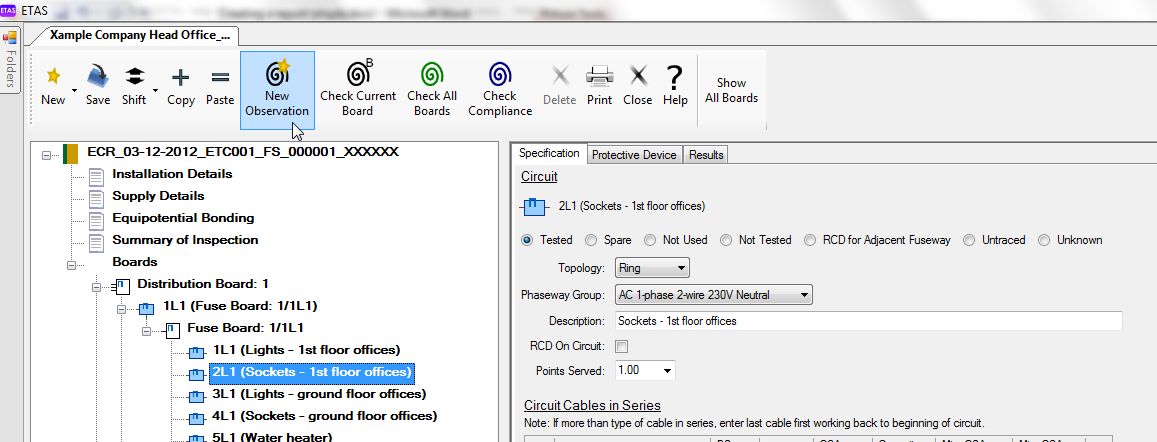
- This example observation relates to the fuse board and not to specific circuit(s) as denoted by the “lit” icon in blue. If you wish to enter an observation against one or more circuits “click” in the Circuits icon which will be confirmed by being “lit” blue.
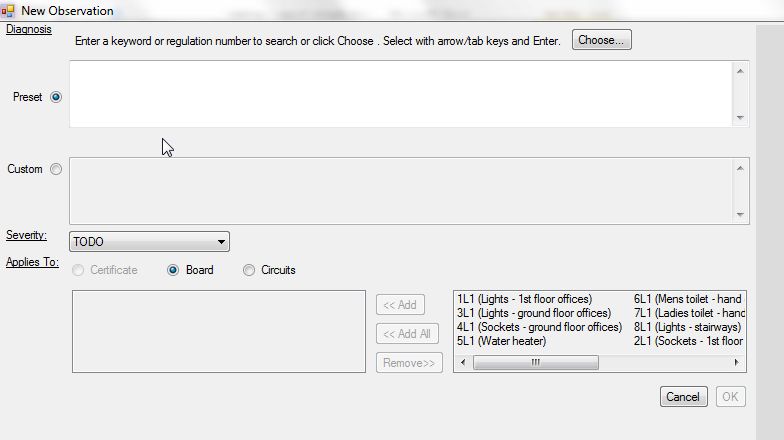
- Start typing a word that is in the observation wording required.
- All the observations containing that word will appear listed on the right hand side. There are also “hot” words that may be typed which will list the relevant observation - for example, if you wanted to bring up observation “Electrical equipment / accessory(s) broken exposing live parts. Regulations 416.2.1, 421.7 & 526.5” you can type in “smashed” or “damaged”.
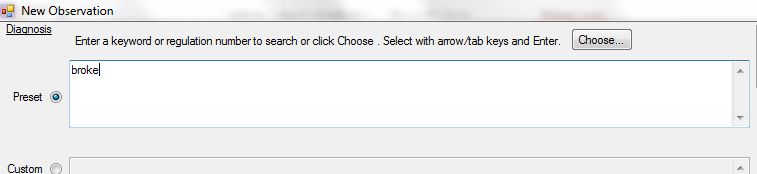
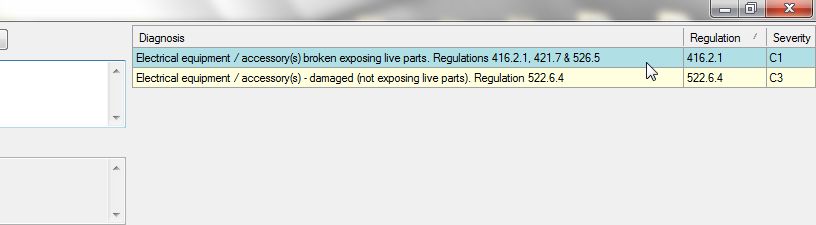
- Click on the most relevant “Diagnosis” and it will appear in the “Preset” pane.
You can also type in the relevant regulation number or part of - for example, to list all the observations relating to a Special Location, type “702” and all the observations listed relating to Special Location 702 Swimming pools and other basins will be shown.
This is also an excellent way for use as a check list, because a full list of non-compliances are shown when dealing with Special Locations to ensure observations relating to non-compliances are not missed.
If you wanted to change the wording of any “Preset” observation for extra clarity - for example, when you have picked the closest observation and it is in the “Preset” box on the left hand side, you can alter it (the wording must be relevant, because once entered and assigned it will, if able, alter the relevant field in the Schedule of Inspections”). High-light the wording to be changed and over-type with the required wording.
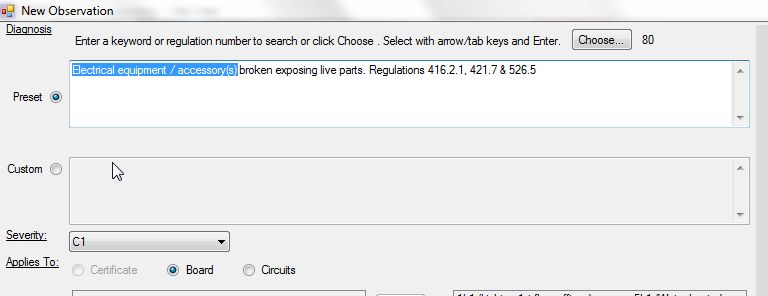
As this does not relate to any circuit(s) ensure that “Applies To” = “Board” which will be lit.
This preset observation has a default severity of C1. If you want to change the severity, then choose the appropriate severity from the drop down box.
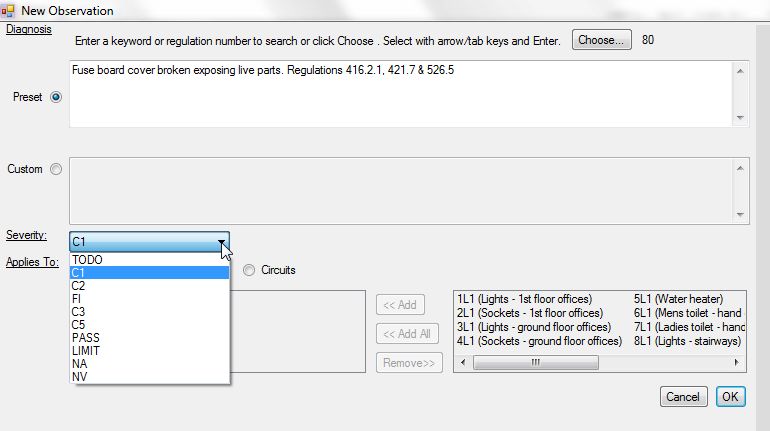
Add a Circuit Observation¶
Now we will apply an observation to one or more circuits.
- Select the board or circuit to which you intend to apply an observation.
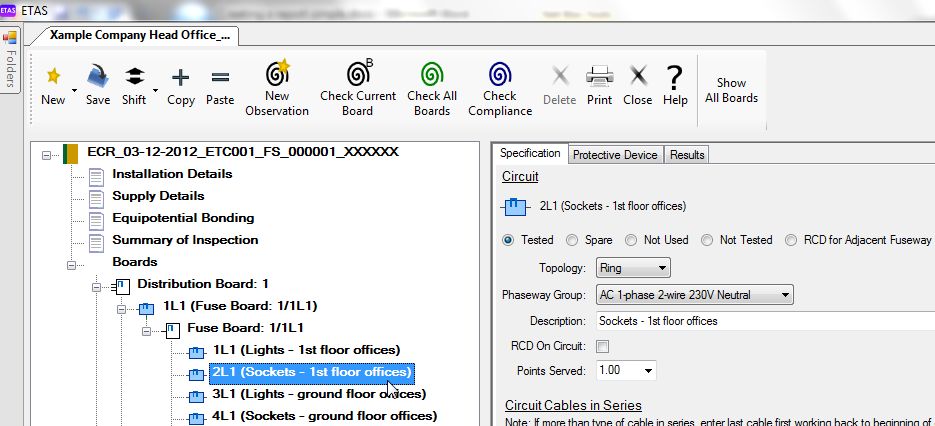
- Click the |new observation icon| button on the toolbar, or click “New” in the Assigned Observations window if it is open.
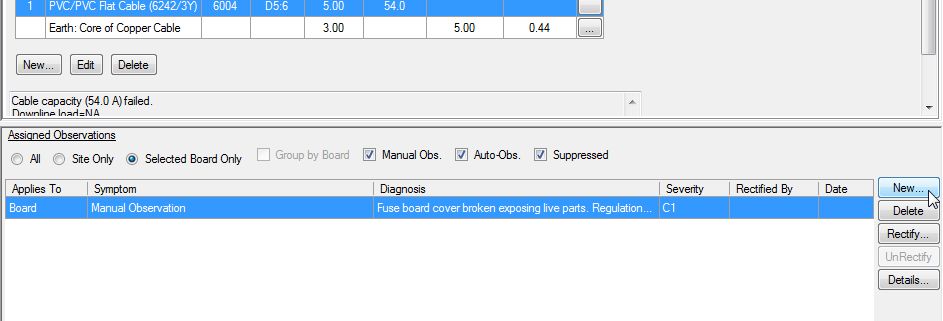
- Let us apply an observation relating to lack of earth sleeving within accessories on circuits 2L1 and 7L1. Start typing in a relevant word, in this case “sle” and all the observations relating or having the word sleeving in appear on the right hand side.
Note:
Sleeving is a commonly misspelled word (sleaving), therefore, if you inadvertently type “sleav”, this is a “hot” word which will bring up the required “Diagnosis”.
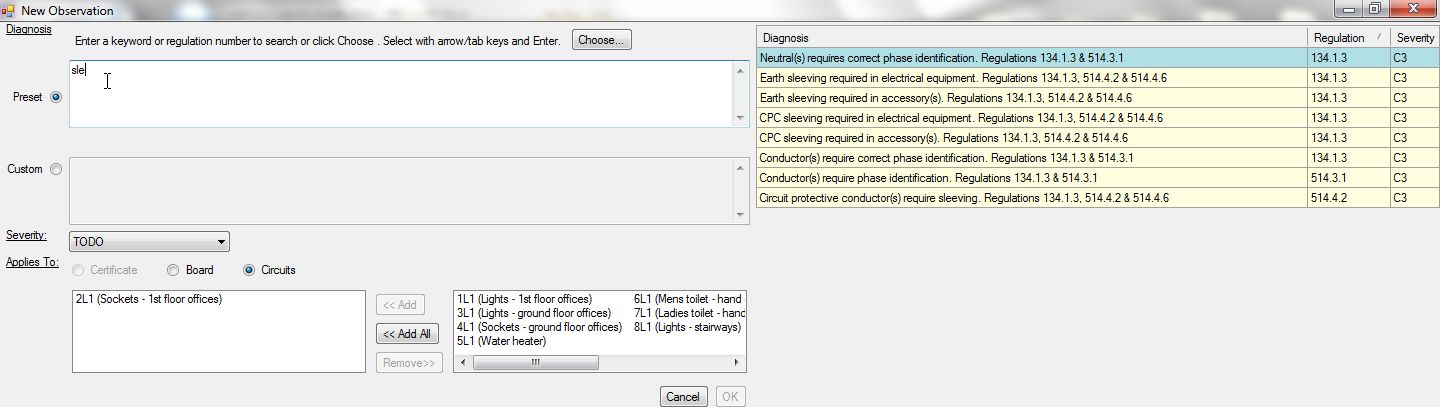
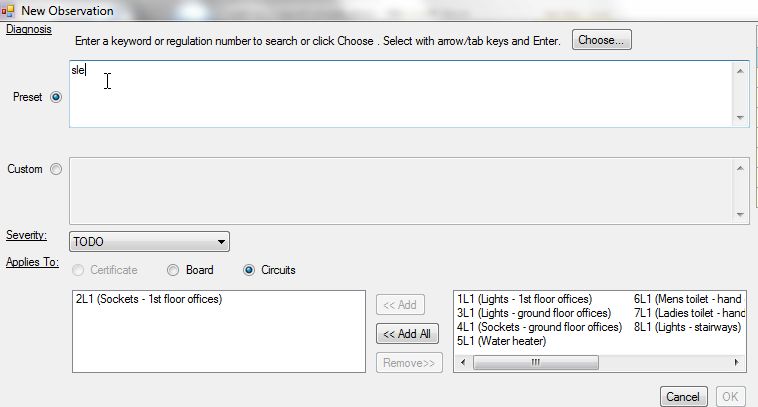
- As fuseway 2L1 has been already highlighted in the left hand pane above, the “Circuits” button in the left hand pane is selected - if you had selected the fuse board, no circuits would have been pre-chosen.
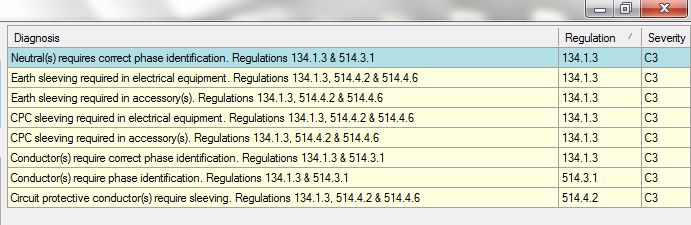
- As circuit 2L1 is already in the left hand pane go to the right hand pane, pick circuit 7L1 and click on “Add”.
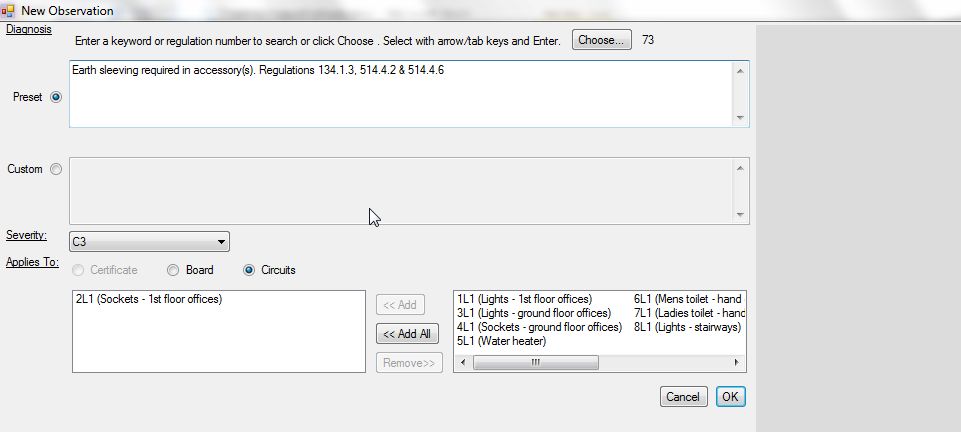
- If the wrong circuit is in the left hand pane then highlight the circuit in the left hand pane and click on “Remove”.
Note:
If you have more than one circuit with the same observation you can either, highlight the first circuit and holding the keyboard “up” arrow key (above the control key) go to the last circuit and the complete range will be highlighted, ready for “Adding”, or high-light the first circuit and keeping the keyboard “control” key pressed, choose individual circuits to be “Added”. Once the correct circuits are in the left hand pane and you are happy with the observation and “Severity” click “OK”.
➲ Next: Create a 3-Phase Board.