Gressingham Foods
Sustainable Waste Management
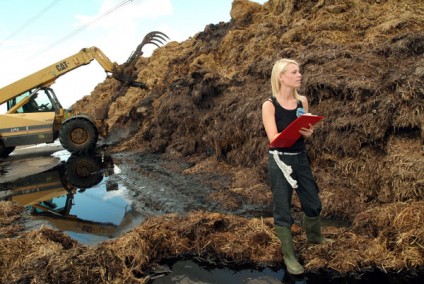
Description and aims
The company breeds, hatches, grows and processes its duck products within a small area of East Anglia. Its factory is based within a three-acre site in rural Suffolk and its farms represent a total of 300 acres. Gressingham Foods is a family-run SME (small to medium-sized enterprise) operating in a highly competitive market. The company recognised the need for greater efficiencies and a more streamlined and modern approach to its business. Gressingham Foods looked to The University of Northampton and the School of Applied Sciences for guidance. The aim was to design and implement an environmental strategy which would reduce waste and result in greater efficiencies and cost savings.
About Gressingham Foods
The business, which was formerly known as Green Label Foods, was founded in 1971 and is the only company licensed to produce the unique Gressingham breed of ducks. The company changed its name in 2006 to better reflect the nature of its best selling product. Duck products are supplied to the catering and retail trade both under its own brands and those of supermarkets.
How the project is being undertaken
The project was undertaken through a Knowledge Transfer Partnership.
Impacts and benefits
The project has enabled Gressingham Foods to meet its objective of setting up a fully integrated environmental strategy. This systematic approach to waste management and resource efficiency has been introduced to all areas of the business. The new approach has helped the company to reduce its waste, water and energy costs as well as minimising the environmental impact of the business. Improved operations have reduced many of the input costs (such as for energy and packaging) and streamlined the removal of waste from the production area, enabling 43% of general waste to be diverted away from landfill. A key factor in the success of the project has been the installation of an integrated water treatment plant.
The company has also established a water testing laboratory to continue the savings made in water testing and treatment costs. The company now has a good understanding of current waste management practice. It has adapted to meet current and impending legislation. In addition, the implementation of a formal environmental management system has helped the company to embed environmental best practice into its core business activities. Introducing
the new approach to operational procedures and providing staff training have further helped to foster a modern culture of new ideas to enhance the business. The company has benefited from total cost savings of £190,000 during the project, comprising £80,000 in the first year and £110,000 in the second year. These savings are predicted to continue year on year.
For more information about the project
If you would like to hear more about this project, please contact Gemma Wickert, Business Development Officer at The Knowledge Exchange.
University
Academic Lead
Dr Margaret Bates
Contact
01604 893230