Davis Derby Ltd
Product Design
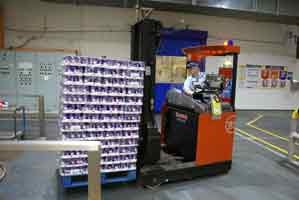
Description and aims
To meet customer and industry demands for safer vehicle operations in logistics centres, mines and quarries, Davis Derby wanted to design a product to improve the safety of pedestrians working in the vicinity of vehicles used in logistics/warehousing and quarrying/mining. Specifically, the purpose of the new product is to identify pedestrians within 5 metres of a mobile plant and to provide a warning to the mobile plant control system so that drivers are alerted to the problem and automatic control systems can be triggered. This product will be known as the Pedestrian Recognition System (PRS).
Each of the two target industries presents is own challenges and criteria requiring separate versions of the PRS:
- In logistics environments, forklift trucks are small (1mx1m), fast and very agile – these will use the PRS-L product.
- Underground mining and quarrying settings may have larger plant (4mx6m) where the driver can not see all sides of the vehicle from the driving position and the equipment requires testing/certification to show it is intrinsically safe. This will use the PRS-QM system.
About Davis Derby Ltd
Davis Derby Limited, based in Derby since 1993, is a long established designer and manufacturer of intrinsically safe electronics and explosion-proof electrical equipment which is designed for use in underground coalmining and other hazardous or demanding situations. Davis Derby is also a leading provider of off-road vehicle driver access control and fleet management information systems, with products in service across the world in a variety of mining and arduous environments.
Known since the early 1800’s as a maker of lamps and other devices maximising the safety of mines and miners, Davis Derby has faced a multitude of challenges over the years as mining processes and the characteristics of other hazardous environments have evolved.
At the same time, the company’s ability to innovate has enabled it to develop technologies that enhance safety and productivity in many other working environments where conveyors, forklift trucks and other bulk handling equipment is present.
How the project is being undertaken
Davis Derby Limited and the Faculty of Arts, Design and Technology at the University of Derby worked together to assess the challenges which the company faces in this particular segment of its market. As a result of that analysis it was decided to submit a detailed proposal for a Knowledge Transfer Partnership (KTP) that specified the company activities, the strategic objectives for company growth in the challenge area, the University of Derby expertise, detailed implementation plan and project plan together with the expected Return on Investment to be made by the company. This proposal was approved.
The project team has jointly recruited a high calibre recent graduate to be the lead designer for the 2 year programme. The designer will work for the university for 2 years and will then be offered a full time role within the company having undertaken an accelerated management programme during this time.
The designer will work with company and academic supervisors to manage and progress the project throughout its implementation to meet the specified partnership objectives.
The KTP will:
- Identify the problems
- Investigate new techniques for the PRS that will be tested against user requirements
- Implement a chosen strategy to provide an engineered market solution for both PRS-L and PRS-QM.
Impacts and benefits
The PRS will provide an input to the fork lift truck indicating the presence of pedestrians: the mobile plant supplier will be responsible for implementing a strategy to control the vehicle. The proposed system is therefore capable of being supplied to OEM plant suppliers as initial fit or as a retrofit to all existing plants that could be modified to process the warning signal. Davis already works closely with OEMs to integrate its current safety systems into mobile plant and would expect to do the same for this new product.
The result of this KTP will address and improve the startling accident statistics caused by the use of fork lift trucks. In September 2009, David Ellison, Chief Executive of the Fork Lift Truck Association, stated ‘With over 400 hospitalisations a year, major fork lift truck accidents happen literally every day in the UK. Most are avoidable, and usually the victim is NOT the truck’s operator.
These are major, life-shattering injuries like crushings and amputations. Last year, ten people were killed – and with fork lifts working on an estimated 100,000 UK sites, literally anyone could be at risk.’ (Figures based on Health and Safety Executive statistics between 2001 and 2008.)
The personal and financial cost of these accidents is large and this product will contribute significantly to a reduction in incidents, benefiting both those working in these dangerous environments and their employers.
For more information about the project
For more information please contact Harold Convey on 01332 593109 or at h.convey@derby.ac.uk.
Duration
2 years
University
Academic Lead
John Redgate
Art Design and Technology (ADT
Contact
01332 593109